INSIGHT
Ⅰ. Forging Classification and Comparison
Forging is a type of metal plastic forming method, and cold forging (commonly referred to as “cold forming”) is a branch of the forging process. Compared to other processes such as casting, the metal flow lines in forging are continuous, resulting in a more compact metal structure in the forged workpiece. This makes it less prone to internal voids and gives it higher strength.
As one of the oldest metalworking methods, forging dating back 6,000 years to ancient Egyptian and Mesopotamian civilizations. The main forging processes include: free forging, die forging, and extrusion forging. Additionally, forging can be classified based on the temperature during processing into: cold forging, hot forging, and warm forging.
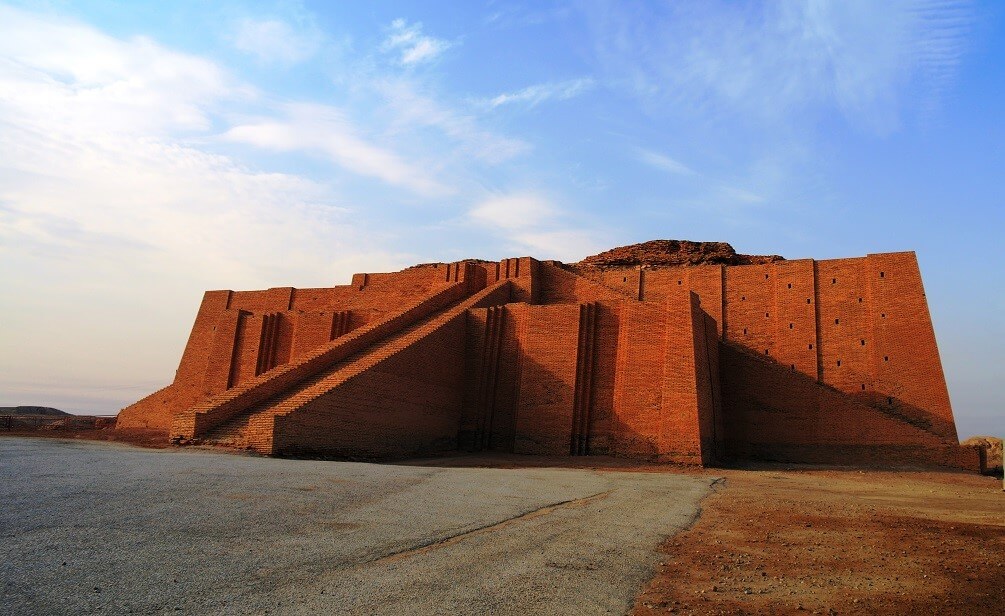
Classification
A. Cold Forming: Cold forming is performed at room temperature under high pressure. It produces products with extremely high dimensional accuracy and smooth surfaces but requires advanced forming equipment and tools. As the degree of deformation increases, the metal undergoes work hardening, which enhances its strength and hardness while reducing ductility and toughness.
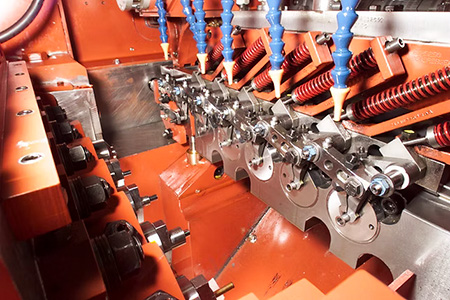
B. Hot Forging: Hot forging is performed at temperatures above the material’s recrystallization point. The high temperature makes the metal very soft, allowing for significant deformation. However, the high temperature also causes oxidation of the metal, which typically results in lower dimensional accuracy of the product.
C. Warm Forging: Warm forging is performed at an intermediate temperature between cold and hot forging. It is a compromise that combines the high precision of cold forging with the ease of processing of hot forging.
▼ The differences between various metal forming processes can be summarized in the following simple comparison:
CATEGORY | COLD FORMING | WARM FORGING | HOT FORGING |
Temperature | Room Temperature | 300 - 700 ℃ | 1100 - 1200 ℃ |
Load | High | Medium | Low |
Processing Size | Small | Medium | Large |
Production Efficiency | ✦✦✦ | ✦✦ | ✦ |
Processing Precision | ✦✦✦ | ✦✦ | ✦ |
Surface Finish | ✦✦✦ | ✦✦ | ✦ |
Near-net Shape | ✦✦✦ | ✦✦ | ✦ |
Energy Efficiency | ✦✦✦ | ✦ | ✦ |
Ⅱ. Comparison of Cold Forming with Other Forming Methods
Cold forming is just one of many metal forming processes. Other forming methods include cutting (machining), casting, sintering, and more:
Cutting Forming (Machining): Shapes the material by cutting it with tools. It is suitable for small-batch, diversified production, offering high precision but lower production efficiency. Compared to other forming methods, material utilization is relatively low.
Casting Forming: Molten metal is poured into a mold and allowed to cool and harden to achieve the desired shape. The precision and surface quality are influenced by the cooling process, and internal voids can easily form.
Sintering Forming: Metal powder is compacted in a mold and then baked at a temperature below the material’s melting point for an extended period to form the final shape. Sintering takes a long time and is suitable for processing small batches of complex shapes with relatively high precision.
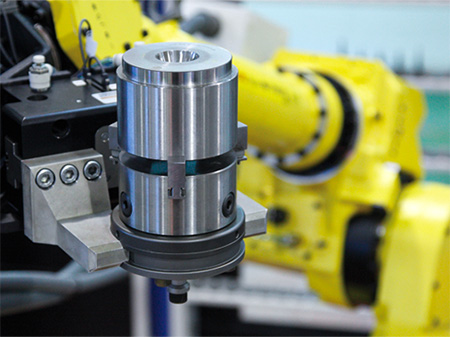
▼ The differences between various metal forming processes can be summarized in the following simple comparison:
CATEGORY | COLD FORMING | CUTTING | CASTING | SINTERING |
Need for Mold | YES | NO | YES | YES |
Production Efficiency | ✦✦✦ | ✦ | ✦✦ | ✦✦ |
Product Precision | ✦✦ | ✦✦✦ | ✦ | ✦✦ |
Product Strength | ✦✦✦ | ✦✦ | ✦ | ✦ |