PRINCIPAL
About Cold Forming
Cold forming is a high-speed forging and plastic forming process conducted at room temperature. It involves precisely shearing metal wire stock to predetermined lengths, then reshaping it into target components through sequential extrusion in a series of tooling cavities. Compared to other machining methods, cold forming technology offers distinct advantages, including high precision, exceptional production efficiency, and superior surface finish quality.
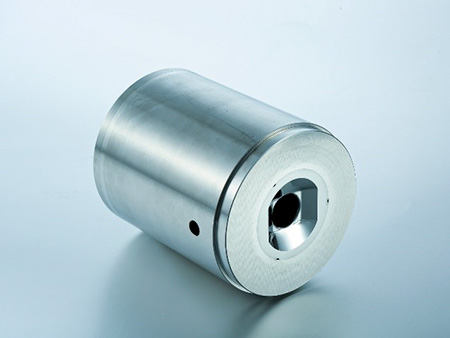
Basic Steps of Cold Forming
A. Forward Extrusion
Forward extrusion is a forming method that stretches the material by reducing its diameter. First, the material (usually a metal rod) is placed inside the cavity of the die. The cold forging equipment applies high pressure to one side of the material through a punch and a mandrel, causing the material to flow in the direction of the punch’s movement into the main die (i.e., forward), forming a product with the desired shape and dimensions.
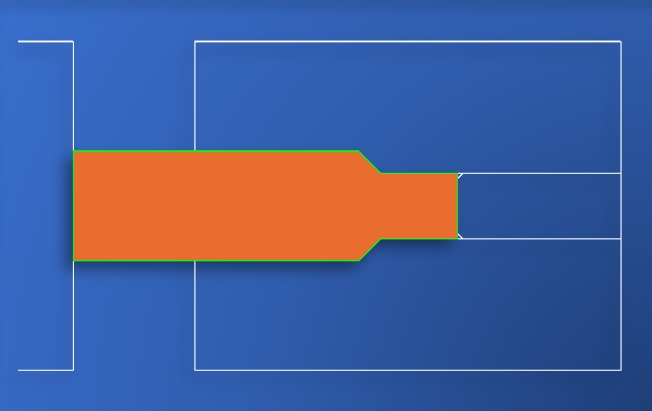
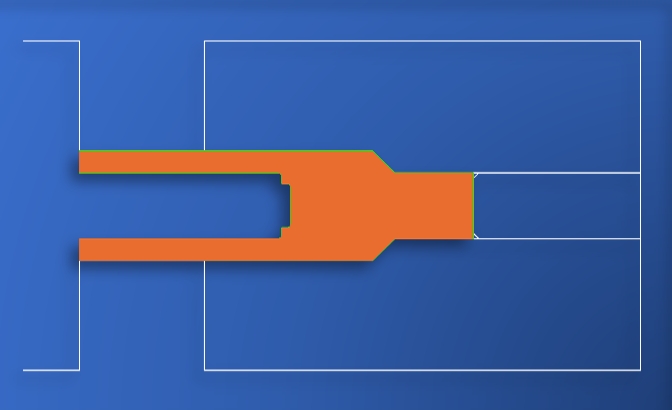
B. Backward Extrusion
Backward extrusion is similar to forward extrusion. The cold forging equipment applies pressure to the material inside the die cavity through a punch and a mandrel. However, the material flows along the edge of the mandrel in the opposite direction to the punch’s movement into the main die (i.e., backward), forming a product with the desired shape and dimensions.
C. Upsetting
Upsetting is a forming method that reduces the length of the material while increasing its local diameter. The material is subjected to radial flow when pressure is applied by the punch on the outer side of the main die (i.e., the die face). This process forms a product with the desired shape and dimensions.
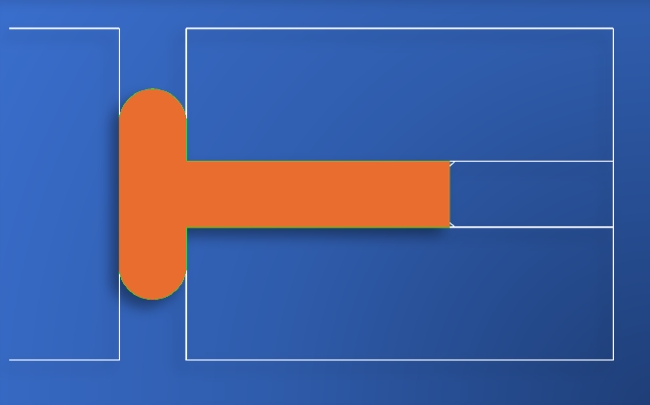
Advantages and Limitations of Cold Forming
A. Advantages
1.Energy Efficiency and Environmental Friendliness : Cold forming does not require a heating process, which saves energy and reduces manufacturing costs while being environmentally friendly.
2.High Dimensional Accuracy : One of the main advantages of cold forming is the extremely high dimensional accuracy of the processed products. Since the process occurs at room temperature, the dimensions of the formed product are not significantly affected by thermal expansion or contraction, ensuring very precise tolerances.
3.Good Surface Finish : During the extrusion process in cold forming, the metal’s crystalline structure is refined, and no oxide layer forms, resulting in a smooth surface finish for the processed product. This reduces the need for subsequent surface treatment steps.
4.High Processing Efficiency : Cold forming shapes materials through die extrusion in a simple and efficient process. Since it is performed at room temperature, there is no need for heating or cooling. For mass production, this provides high processing efficiency, thereby reducing manufacturing costs.
5.Material Savings : Compared to machining, cold forming generates almost no waste material, or only minimal waste. With the same amount of raw material, more products can be manufactured through cold forming, lowering overall production costs.
6.Near Net Shape : Products formed through cold forming are nearly finished and require little to no additional processing. This eliminates some secondary operations, further reducing manufacturing costs.
7.Improved Mechanical Properties : During the cold forming process, the raw material undergoes work hardening, and the metal grains remain intact during flow. As a result, the processed products exhibit excellent mechanical properties, such as higher strength and hardness.
B. Limitations
1.High Tooling Costs : Achieving the high dimensional accuracy of cold forming requires equally precise and highly durable molds, which can reduce the frequency of mold replacement. However, this makes the initial cost relatively high for small-batch production or short-term projects. Cold forming is better suited for large-scale, long-term, and stable projects.
2.Long Mold Change and Setup Time : The setup and debugging of equipment and molds before cold forming can take a significant amount of time. Improper mold design or manufacturing, or incorrect equipment adjustments, may affect production efficiency. Therefore, cold forming is more suitable for long-term, stable projects.
3.Shape Restrictions : The feasibility of cold forming depends on the material properties, the structure of the cold forming equipment, and the symmetry of the product shape. High material hardness (which causes tool wear), limitations in the equipment’s transfer mechanisms or ejection systems, and asymmetrical product shapes may make certain designs unsuitable for cold forming.
4.Difficulty in Secondary Processing : For products that require secondary processing after forming, the work hardening that occurs during cold forming reduces ductility and toughness. Additionally, residual stresses within the formed product may cause bending or deformation during secondary processing, making it less favorable for post-processing operations.